Business sectors
Operations strategy
The strategic transformation of operations is a complex process that requires a cross-functional approach to value chains, integrating technological, organisational and human aspects. By embarking on this path of transformation, companies aim to improve their competitiveness, agility and ability to respond to changing market needs.
Your challenges
While it’s sometimes easy to chart a company’s course, the path to get there can be more arduous. Capitalising on your strengths, adapting to real and likely changes, and developing your resilience are the challenges you face.
Benchmark and competitivenes
- Assessing yourself against the market
- Assessing yourself against the market
- S’assurer que les investissements et efforts soient correctement ciblés
Value chain resilience
- Reconciling resilience and economic performance (sourcing, production or distribution strategy)
- Searching for the most efficient scheme by studying alternative
Sustainable performance
- Seek constant performance by increasing income or reducing costs, with a full-cost vision
- Gain productivity points
- Reduce industrial and logistics costs
- Enable the development of new products or services
Ability to transform
- Defining the most appropriate organisation for the issues to be addressed
- Reconciling the ability to commit human and financial resources to finance the transformation
- Have a quantified roadmap with milestones, for regular monitoring and adjustments, based on a tangible ROI
Our conviction
Scripting and anticipating risks
- The development of different scenarios makes it possible to objectively assess projected situations according to quantitative and qualitative evaluation criteria.
- In addition to identifying the most appropriate alternatives, this process helps to prepare the ground for rapid, rational decision-making in the event of a hazard: beyond the plan, its construction also provides a wealth of information for understanding risks and acting accordingly when they arise.
Working towards a global optimum
- Transformation of Operations can take many forms and impact different links in the value chain, as well as different functions within the organisation.
- It is therefore essential to adopt a cross-functional vision of activities and to implement changes that feed into the overall optimisation of Operations, rather than adding up local optimums, which can be detrimental to the overall relevance.
Devising different levels of action
- The transformation roadmap needs to be understood at multiple levels: an overall macro vision to measure the benefits and confirm that the company’s objectives have been achieved, but also an operational approach aimed at the various business lines and departments, with its quick wins, pilot phases and demonstrators.
Involvement at different levels
- Sharing the strategic vision with the CODIR and COMEX is essential to ensure that everyone is on board and to prepare for its flawless application.
- In addition, the appropriate involvement of business experts remains essential, in particular to capture specific irritants, which can then be synthesised to provide a clear understanding of the overall vision.
- The transformation plan requires a degree of co-construction with General Management to ensure that it is adopted by successive appropriations.
Securing project governance
- While the strategic vision and the direction to be taken should be dealt with by the company’s senior management, the governance of the implementation roadmap should also be considered by top management.
- Decisions on reorientation and prioritisation must be taken by all the company’s departments, to ensure that the transformation is carried out with a single, cross-functional voice.
Our solutions
and expertise
If you want to benchmark your performance and your organisation, and design your strategic vision of Operations to transform them, our expertise will support you from strategic definition to operational implementation across the different links in the value chain.
Diagnosis and strategic transformation
- End-to-end supply chain diagnostics
- End-to-end industrial diagnosis
- Strategic support
- Definition of the target organisational model
- Transformation support (quick wins, pilots, etc.)
- Operations dashboard and benchmark
Operations modelling
- Industrial master plan
- Logistics master plan
- Design and development of a digital twin
Business plan, IBP and S&OP strategic vision
- Design and implementation of BP, S&OP/IBP
- Digitalisation of decision-making processes
Sustainable supply chain
- Life cycle analysis and eco-design
- Implementation of circular and use economies
- Ecological and energy transition for industries
- Environmental performance management
Our certifications and training
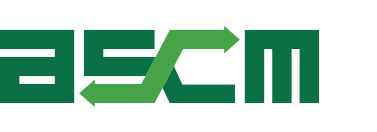
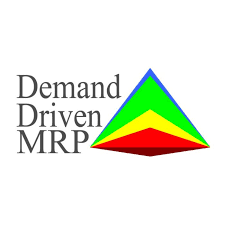
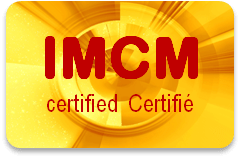
Your gains
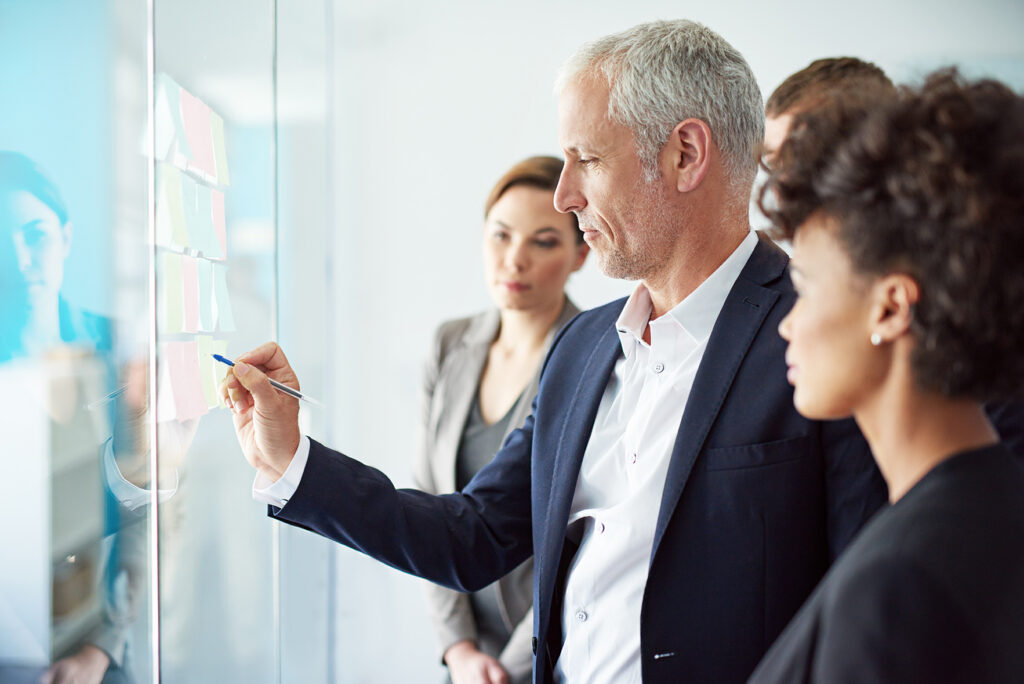
Better use of resources
- Absorption of growth at iso-capacity
- Logistics capacity gains of up to 50
- 10 to 20 points improvement in service rate with customer delivery times
- -50% to 70% at iso-resources
- Optimisation of distribution costs while reducing environmental impact
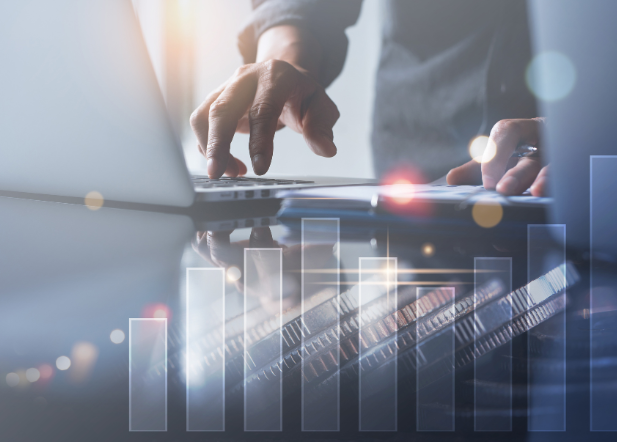
Financial gains
- Reduction in the total cost of the supply chain (Cost to Serve) by 5% to 20%.
- 15% to 20% reduction in supply costs (rationalisation, inbound transport, reduction in inter-site transfers)
- Specific reduction in production costs from 5% to 30%.
- Specific reduction in transport costs: 10% to 25%.
- 5% to 30% reduction in inventories
- 20% to 70% reduction in work-in-progress
- Reduction in excess stock and destruction from 30% to 50%.
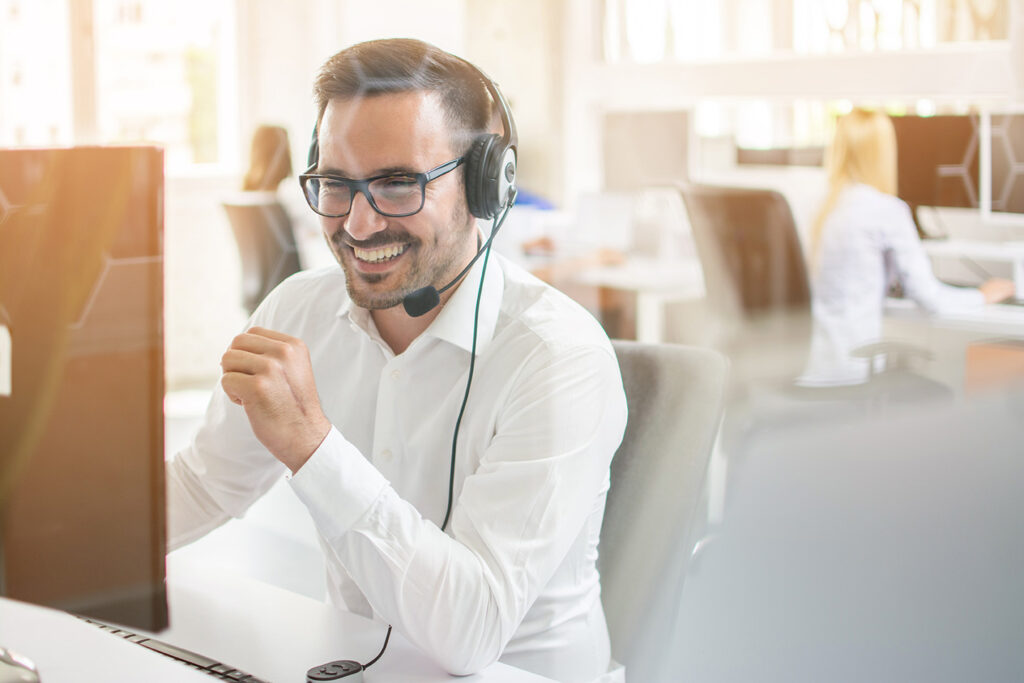
Service and business development
- Improving the service rate by 2 to 5 points
- Definition and implementation of the customer promise
- Ability to absorb exceptional requests by 5% to 10%.
- Absorption of iso-resource growth (human and financial)
- Standardisation of practices to enable the acquisition, integration and synergy of new entities
- Professionalism in Operations, with customers and partners
- Customer-perceived lead times reduced by up to 80%.
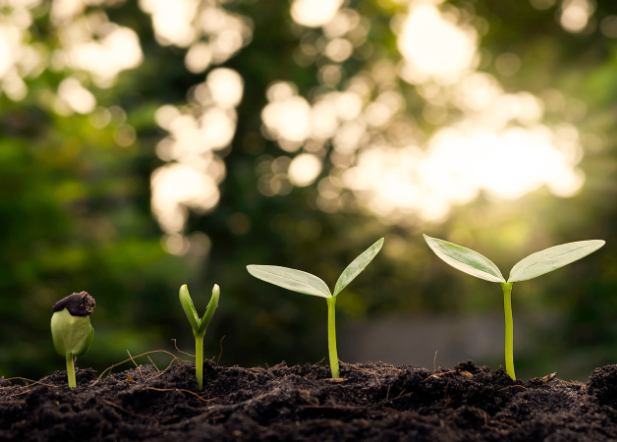
Sustainability and business agility
- Increased supply chain resilience to both hazards and opportunities
20% to 70% reduction in lead times - Assessment of the maturity of the different facets of
- Operations, targets and shared trajectories
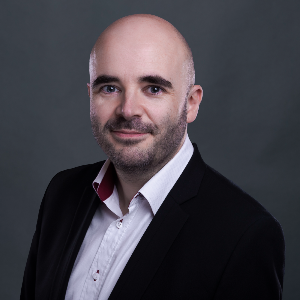
A Project ? Contact us
Partner
With 25 years’ experience in consultancy, some of it international, Nicolas has carried out a wide range of assignments in different business sectors: definition and implementation of industrial progress plans, design of industrial and logistics schemes, Lean Management and supply chain overhaul (flow optimisation, flow and process management).
He has also spoken at a number of conferences on the application of S&OP processes in companies (based on a study carried out in partnership with the French logistics association Aslog), the issue of industrial and logistics relocation or regionalisation, and the evolution of customer service.
Some of our references
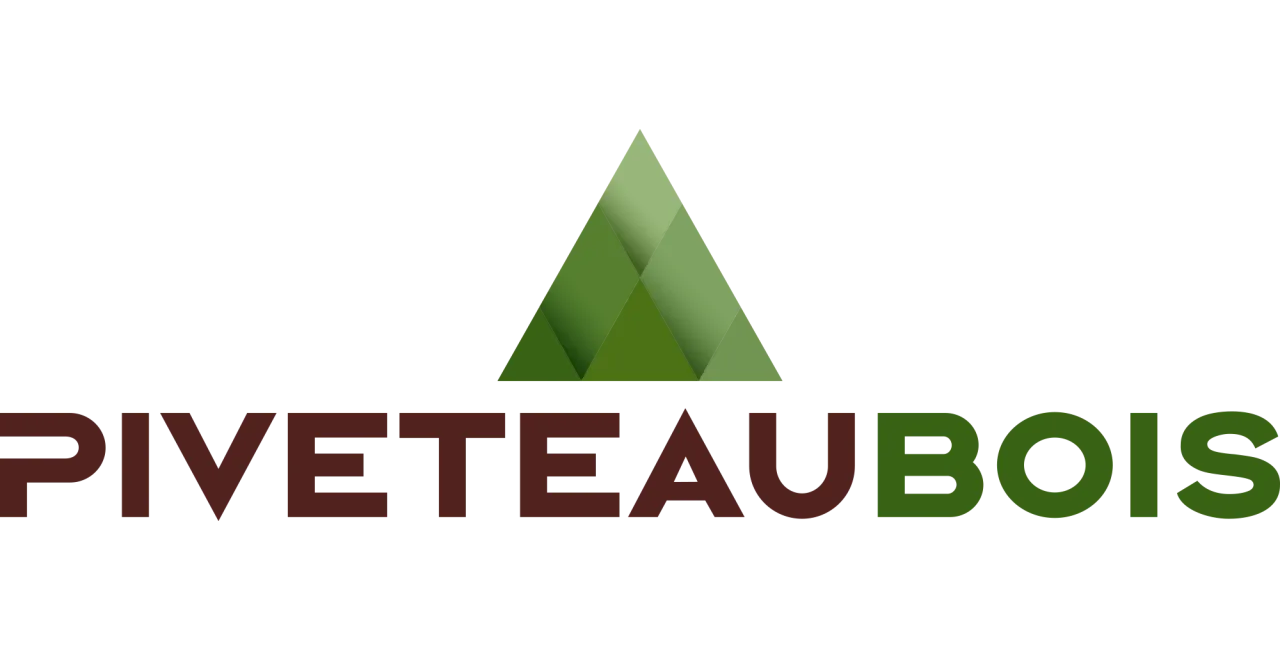
Support for General Management in defining the company's strategy and its implementation by product line and business line over the first 5 years
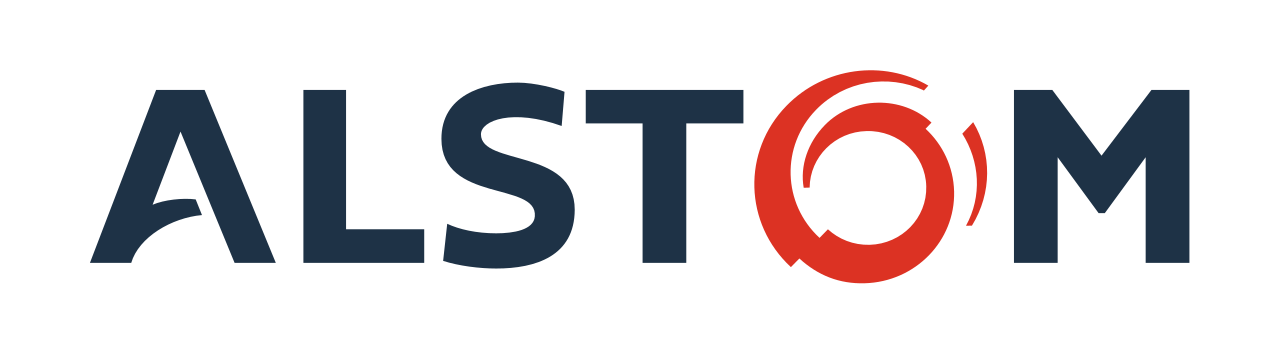
Securing the long-term future of the Suppliers Supply Chain
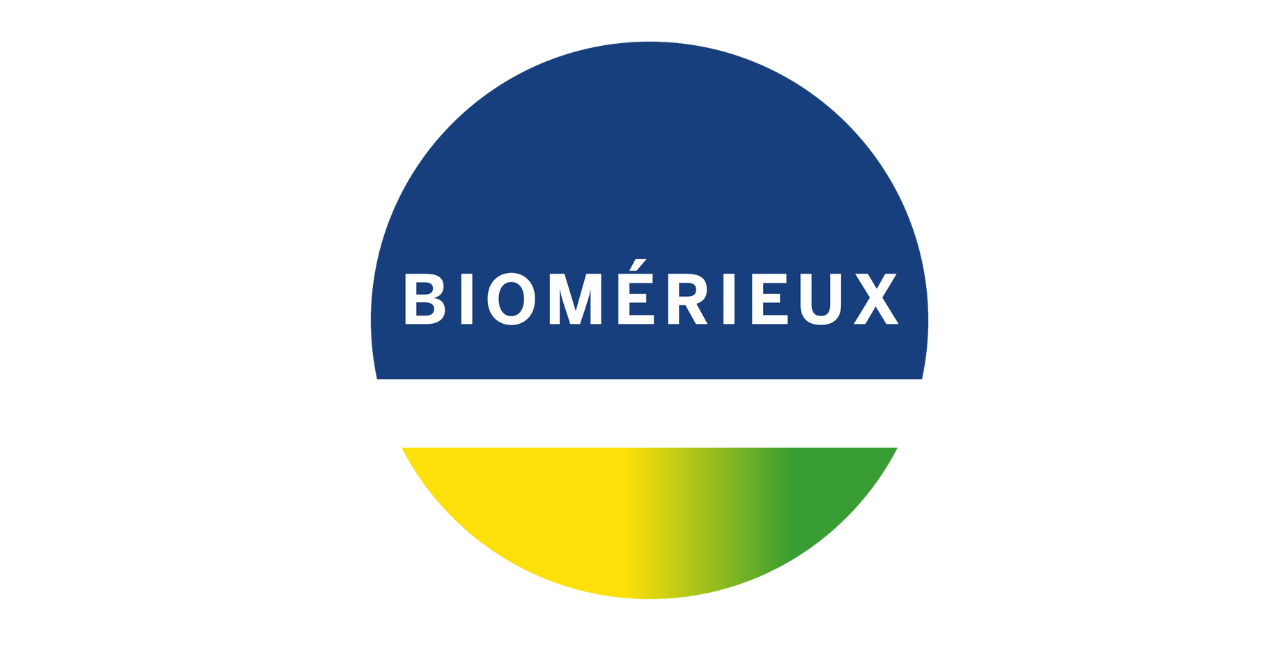
Diagnosis and vision of the Group Supply Chain model, followed by support for its implementation
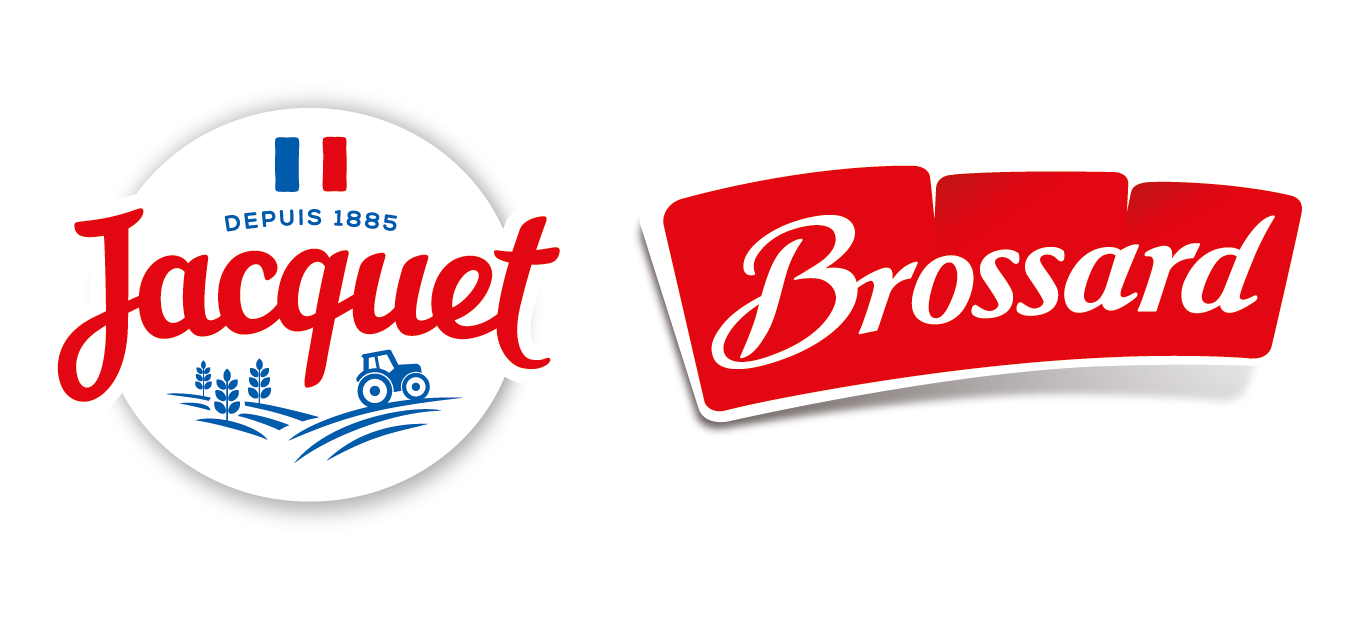
Industrial master plan: resizing of sites and production lines to keep pace with business growth
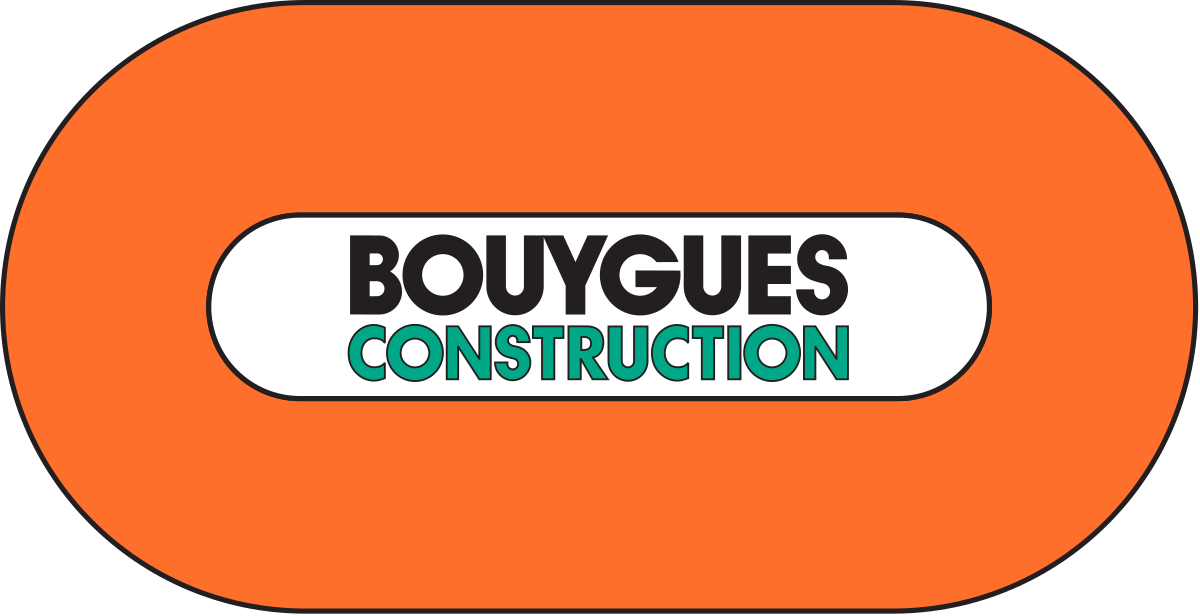
Design of an optimised model for efficient, controlled management of the site supply chain
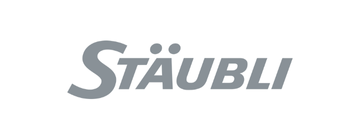
Dimensioning of target industrial and logistics plans for the next 10 years
Use Case
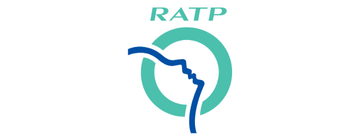
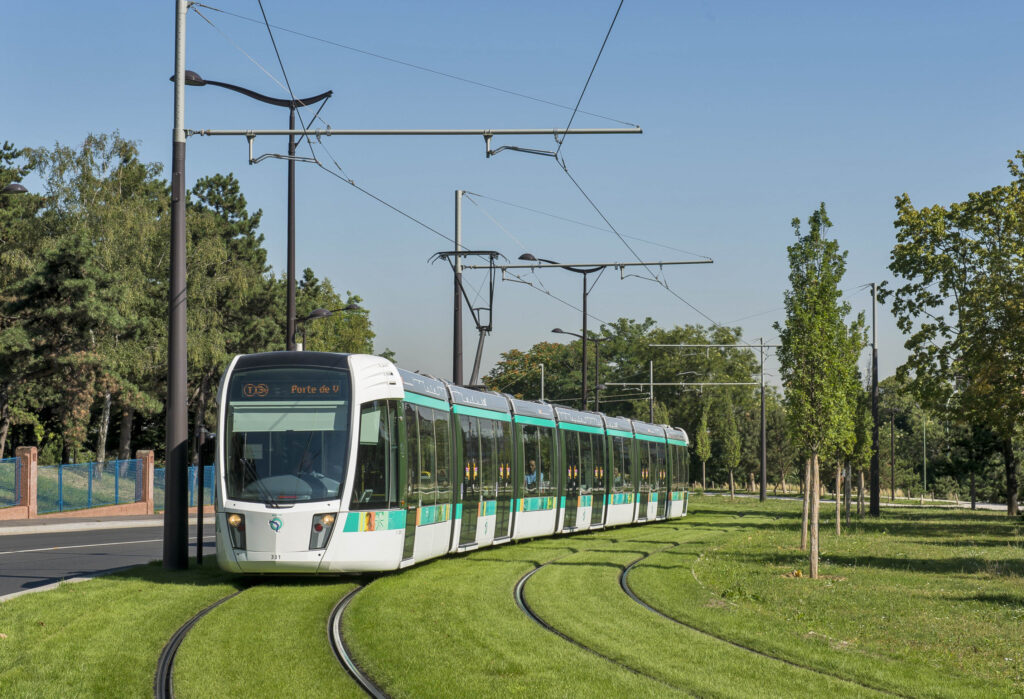
Diagnosis and design of a scenario to improve the logistical and operational performance of the MF67-TW unit
Our intervention
- Scoping and diagnostic phase
- General solution design phase:
- Creation of a logistics cost simulator
- Workshops to design target flows and reorganise the logistics activity
- Definition of project and plant indicators to manage operational activity
- Construction of 3 options per identified project axis with evaluation of associated gains and costs
- Selection of the scenario
The results
- Improvement scenario deployable in 1 year with an ROI of 2.5 years:
- Training and change management for teams
Reduction in advanced and central component stock - Improved productivity by standardising workstations, reducing range times and reducing stock-outs
- Sustainability of the project and continuous improvement of the unit through the creation of an industrial methods function
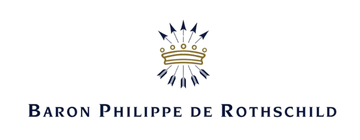
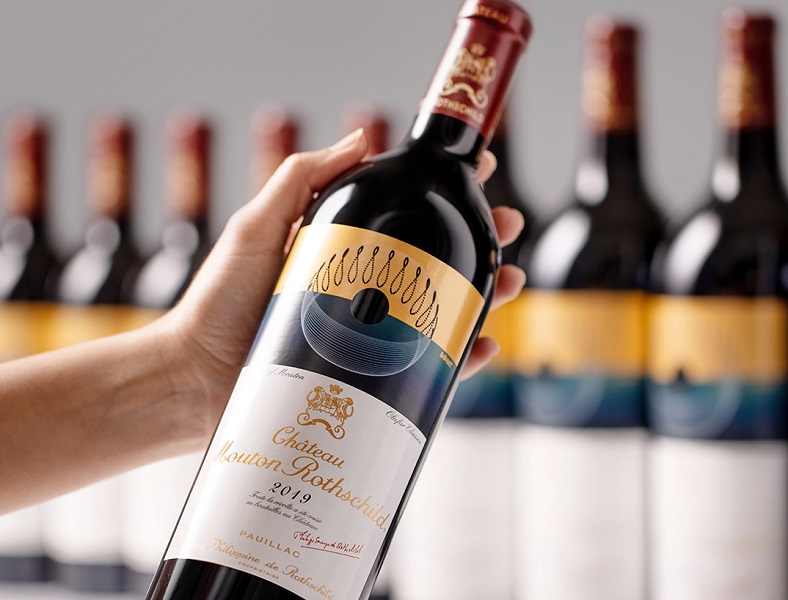
Logistics master plan for the Châteaux grands crus business: resource sizing, security and trajectory
Our intervention
- Modelling of the development of stocks and the logistics activity of the Châteaux division
- Analysis of natural and technological risks
- Identification of expectations in terms of services and security, with the company’s main functions, as well as with its main merchant customers
- Identification of the potential for pooling resources with the other business unit
- Proposal of suitable qualified alternative scenarios by an expert business team
- Development of a transformation path validated by senior management
The results
- Definition of the long-term business volumes of the Châteaux division, taking into account the wine-making and commercial aspects
- Identification of the main risks and means of mitigation
- Definition of alternative logistics scenarios
- Development of a development path validated by general management, with trigger thresholds
They testify
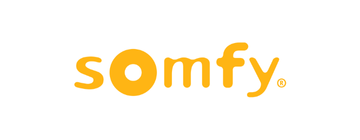
Emmanuel CARMIER,Lean & Change Director, SOMFY Group
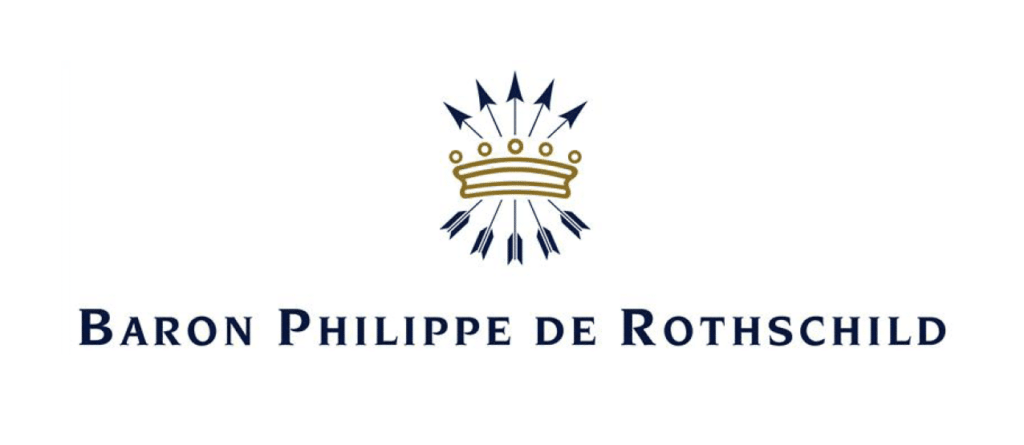
« I found the study carried out by Citwell to be both exhaustive and precise, since all situations were taken into account. »
Eric Tourbier, Director of the Mouton Rothschild technical division of Baron Philippe de Rothschild S.A.
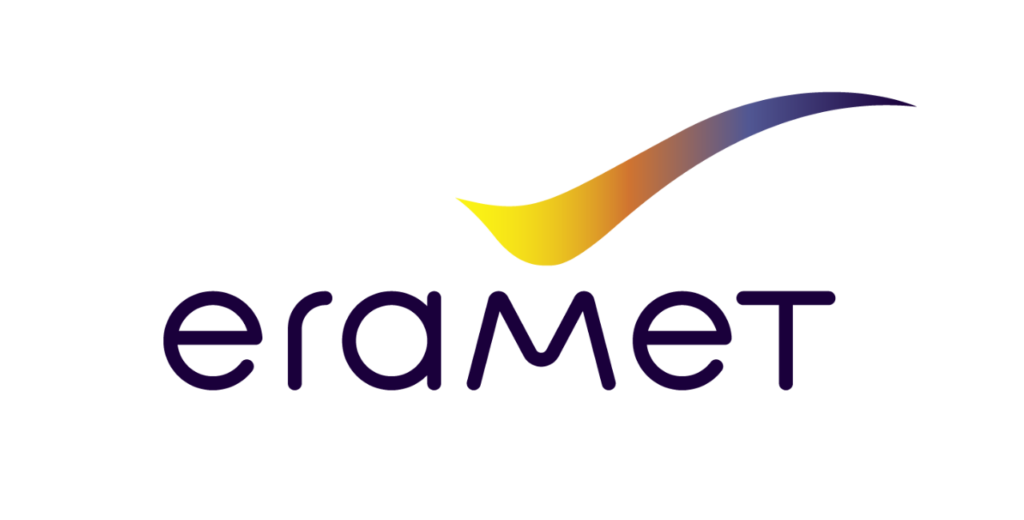
« An innovative method, with deployment of the project coupled with support for the transformation, which has benefited our entire Lean approach. »
Patrick Guillon, Supply Chain Manager of SLN, Eramet Group
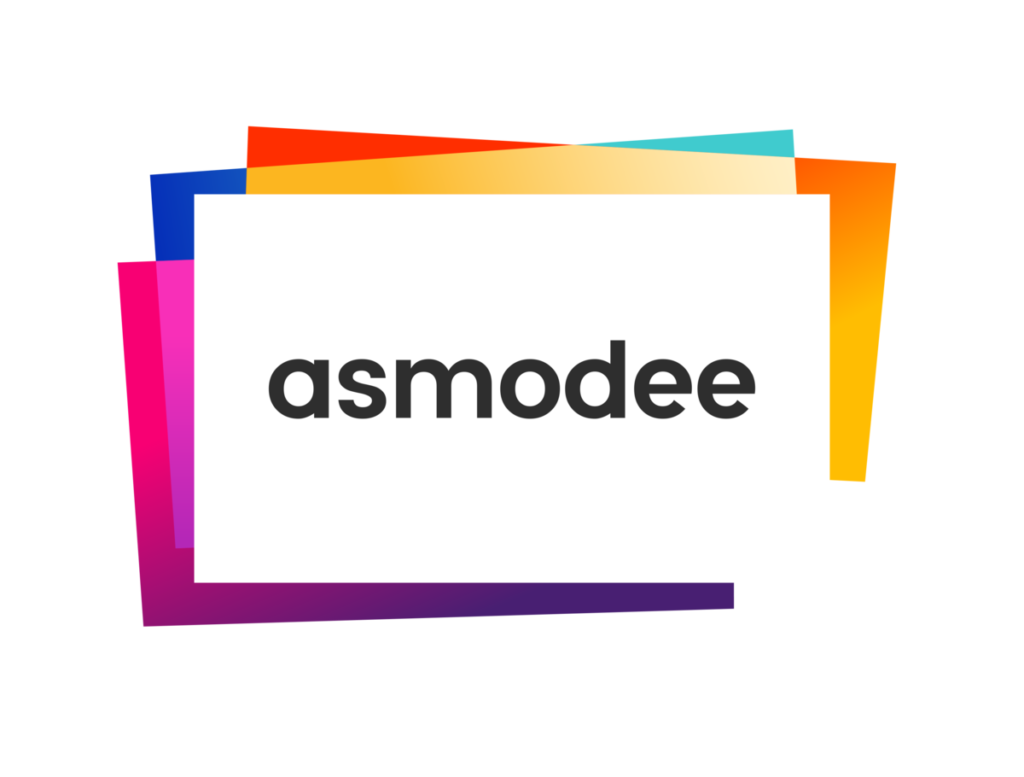
« Thanks to Citwell, we gained a better understanding of our own business. After analysing our processes, they helped us implement a new organisation. »
Christophe Arnoult, Managing Director, France, Asmodee