Business Expertise
Performance of industrial operations
Whether it’s redesigning a low-carbon factory, digitalizing your processes, leading your operational teams, developing performance and quality, etc., we work with you to meet the same challenge: to accelerate the achievement of measurable and sustainable results to ensure your competitiveness and impact your profit and loss account.
Your challenges
In today’s competitive environment, optimising your industrial operations and controlling your resources are crucial to ensuring your growth and long-term future.
Keeping pace with low-carbon industrial sites
- Developing a strategic vision for your equipment
- Managing the ramp-up of new industrial capacity
- Segmenting activities and developing key success factors
- Successfully managing projects involving numerous partners
Committing your organization to creating customer value with Lean Manufacturing
- Spread the lean culture from operator to General Manager
- Implement progress projects and problem-solving tools
- Deploy global, systemic and sustainable progress approaches
- Certify stakeholders and the company
Take the lead in the sector in terms of competitiveness
- Reduce lead times
- Develop capacity
- Improve quality
- Increase material yields
- Ensure productivity growth
- Increase equipment efficiency (OEE)
- Reduce maintenance costs
Develop a strong, positive management culture
- Training your staff
- Implementing managerial routines
- Increase the conviction and skills of your field staff tences vos collaborateurs de terrain
- Coaching your teams towards new practices.
Secure your suppliers' sustainable performance
- Carry out a 360° industrial and financial audit of your supplier panel
- Draw up action plans and prioritised roadmaps
- Support and monitor actions to ensure that progress is actually made
Establish an industrial strategy that genuinely creates value
- Establish and maintain production standards
- Calculate industrial cost prices
- Identify and implement levers for visible progress on the income statemen
- Controlling losses
Our convictions
Creating added value for the customer ... and for stakeholders
Creating added value is the goal at the heart of our practice. Thanks to our expertise in Lean and operational performance, production processes are optimized, flexibility is developed, costs are reduced and product quality is improved. Tailor-made solutions mean increased efficiency, reduced lead times and maximized profitability. Working closely with customers’ needs, growth opportunities are identified and their strategic objectives addressed. A systemic approach guarantees sustainable results and continuous improvement in industrial performance. Each project becomes a story of transformation, where operational excellence is not only targeted, but achieved. A company then becomes a benchmark for resilience and value-creating innovation.
Involving teams in the field in a systemic approach
To achieve operational excellence, we have developed a systems approach for our teams in the field. This approach is structured around four main areas: processes, people and organization, material resources and data, and management. By optimizing processes, we ensure that production runs smoothly and efficiently. By enhancing people and organization, we strengthen commitment and skills. Equipment and data are optimized to ensure maximum use of resources. Finally, rigorous management enables us to monitor performance and adjust actions in real time, ensuring continuous and sustainable improvement.
Streamlining processes to get the best out of operational systems
Maturity, regularity and controlled lead times are the keys to exceptional performance. These levers make it possible to turn challenges into opportunities, by requiring a precise description of processes and a rigorous, quantified assessment of their effectiveness. Continuous development to perfect these processes then becomes a driving force for innovation and progress. Each action mobilises all the energies available within the organization, from management to teams in the field, uniting their efforts towards a common goal. By harmonising practices and aligning everyone’s contributions, a dynamic and inspiring environment is created, where each element plays a crucial role in achieving optimum performance. This approach ensures sustainable operational efficiency and forges a stronger competitive edge, which is visible to customers.
Deploying a methodical approach derived from the Lean culture
Defining value from the customer’s point of view, mapping the value chain, eliminating waste (Muda), creating a continuous flow and establishing a pull system are the foundations of a Lean transformation. Through continuous improvement (Kaizen), every challenge becomes an opportunity for greatness, and every success a step towards excellence. By adopting Lean Manufacturing tools and techniques such as 5S, just-in-time (JIT), kanban, poka-yoke, andon, SMED, and Value Stream Mapping (VSM), Lean transcends methods to embody a true state of mind. It’s not just a series of practices, but a dynamic philosophy where every improvement, however small, forges a path towards real performance. Lean invites everyone in the organisation to see challenges as springboards for innovation, turning every victory into a positive loop.
Mobilizing energies through small and large victories
An Operational Excellence approach requires the mobilization of everyone, from the operator to the CEO and from the CEO to the operator, based on a logic of small, permanent victories. Each victory strengthens commitment and proves that continuous improvement is possible. Support for cultural change and transformation is provided by specific resources tailored to each level of responsibility in the operational chain. This includes tailored training, collaborative workshops and performance monitoring tools. These initiatives help to create an environment where everyone in the organization feels involved and responsible for the collective success. Transparent and regular communication on objectives and progress encourages buy-in and alignment from all players. By incorporating feedback and celebrating successes, we reinforce the culture of excellence and ensure a sustainable and effective transformation, thereby contributing to optimum business performance.
Setting progress in motion all the time
To excel sustainably in a VUCA (volatile, uncertain, complex and ambiguous) environment, a company must embrace perpetual progress. By cultivating constant agility, it becomes capable of adapting quickly to market changes and new customer expectations. By maximizing resource efficiency, frugality transforms every challenge into an opportunity for innovation and growth. Continually measuring ourselves against the benchmarks of excellence in the market helps us to maintain high standards and inspire a relentless quest for perfection. This approach infuses a culture of continuous improvement in which every employee feels part of a shared journey towards excellence. In this way, the company forges a resilient and dynamic identity, ready to overcome obstacles and boldly seize opportunities. By setting progress in motion all the time, it positions itself not just to survive, but to thrive and inspire, guaranteeing sustainable performance and dazzling competitiveness over the long term.
Our solutions
and expertise
Our expertise in lean, industrial design, operational efficiency, cost reduction, training and corporate culture ensures that the expected gains are actually achieved.
Performance implementation
- Industrial and financial audits
- Definition of global and multi-site roadmaps
- Process optimization (digital twins)
- Process optimization (conversion costs)
- Diagnosis and benchmarking of SQCDME performance
- Development of managerial maturity
- Supplier performance development
- Industry 4.0 project management
Deployment of Lean Manufacturing
- Acculturation and conviction building
- Training, green belt and black belt certifications
- Process optimization and development of added value for customers
- Lean progress projects: VSM, 5S, Kaizen, Hoshin, JIT, SMED, TPM, Heijunka, Hoshin Kanri, Gemba
- Systemic approach, from acculturation to organizational alignment and the generation of added value and innovation for customers.
Implementation of Operational Performance Frameworks – SPO
- Establishment of managerial standards
- Deployment of digital visual management
- Skills training for teams, 1st level managerial training, coaching for field managers
- Industry 4.0 project management
Reducing production costs
- Definition of the cost model
- Review of production standards and implementation of maintenance routines over time
- Identification of managerial levers for maintaining economic indicators
- Costing and prioritization of improvement activities
Interim management with our experts on the ground
- Qualification of the expertise required and the level of intervention
- Operational support alongside your teams to deal with an exceptional situation
- Providing the firm’s expertise to support operational activities opérationnelles.
Our certifications and formations
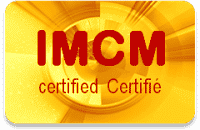
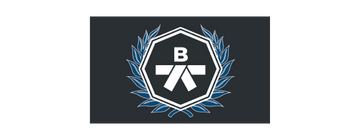
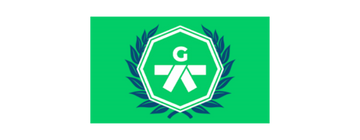
Your gains
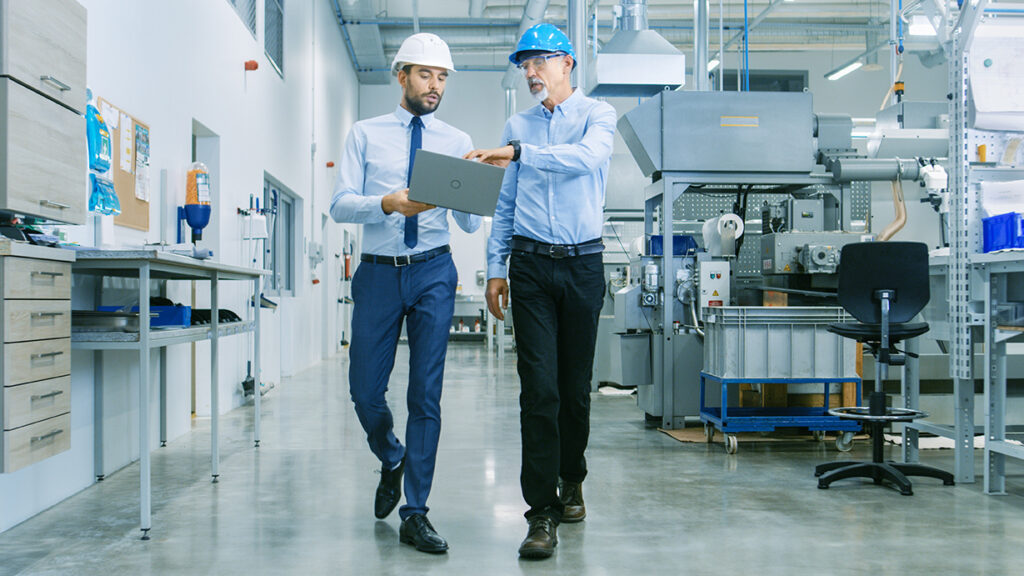
Turning a sustainable corner in operational performance
- Improving customer service levels
- Capacity development
- Reduction in lead times
- Improving quality and GCP
- Reduction in material losses
- Improvement in OEE and productivity
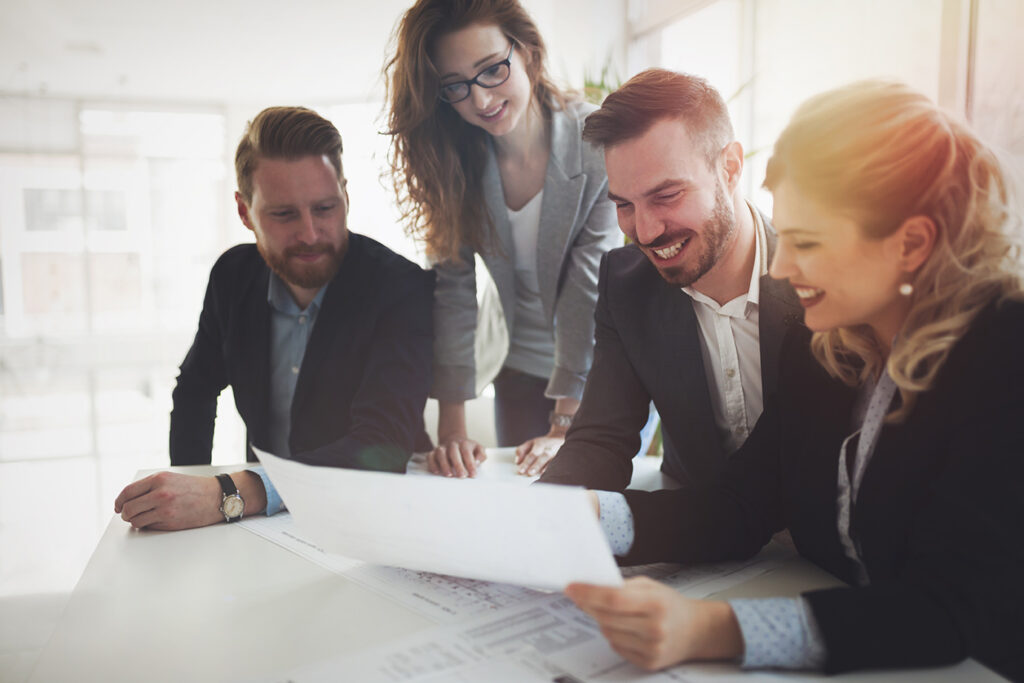
Team resilience and flexibility
- Ability to adapt quickly to changes in the market
- Peace of mind in operating methods
- Improved attractiveness and lower staff turnover
- Reduced absenteeism
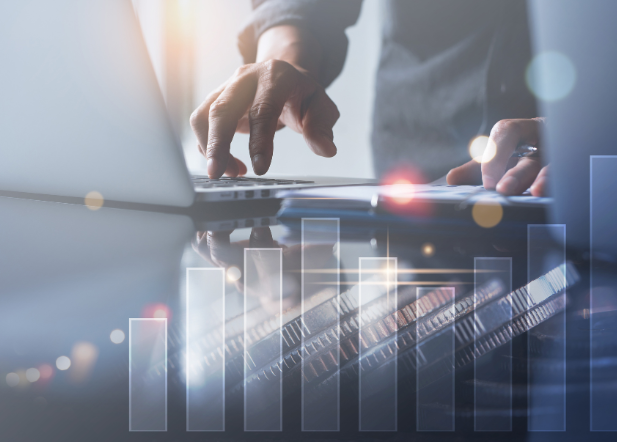
Visible financial gains in the income statement
- Variable costs reduced by 3% to 8%.
- Indirect production costs reduced by up to 10%.
- Reduction in MOD rates through reduced absenteeism
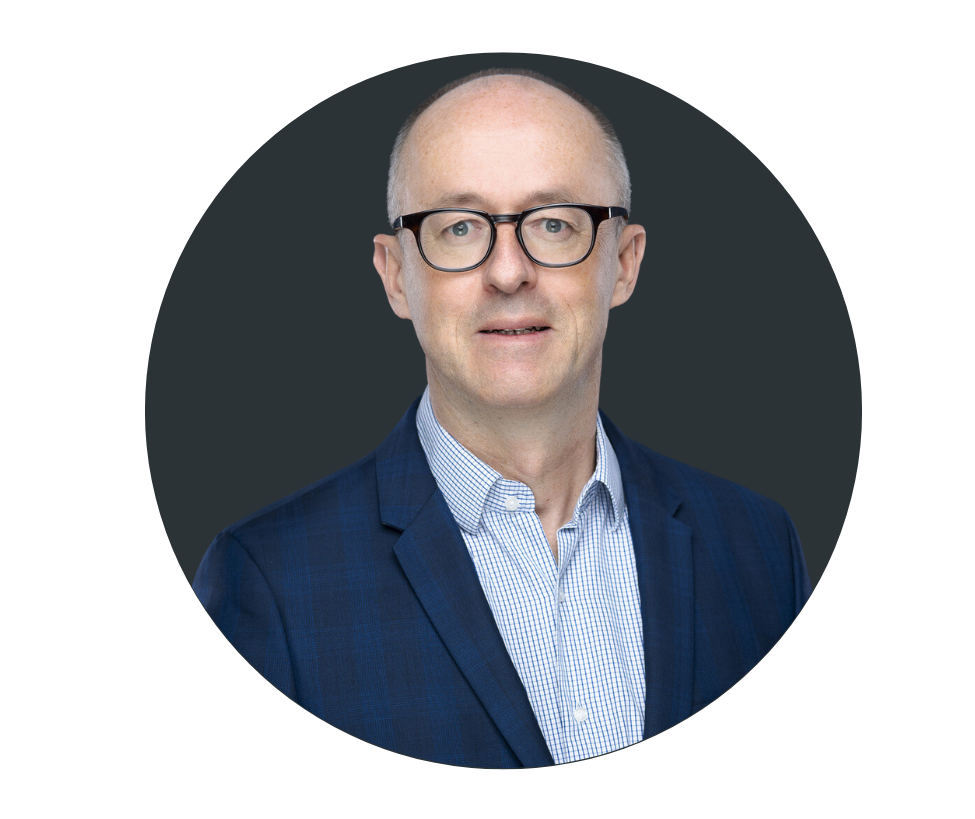
A Project ? Contact us
Partner
After 10 years’ operational experience as Production Manager and then Programme Manager in the aerospace industry on international programmes, Mathieu joined the consultancy business in 2006. A specialist in operational performance and cost control, he helps companies to implement solutions that have a visible impact on the income statement. His areas of expertise include company turnarounds, operational performance including support functions, steering processes and management control.
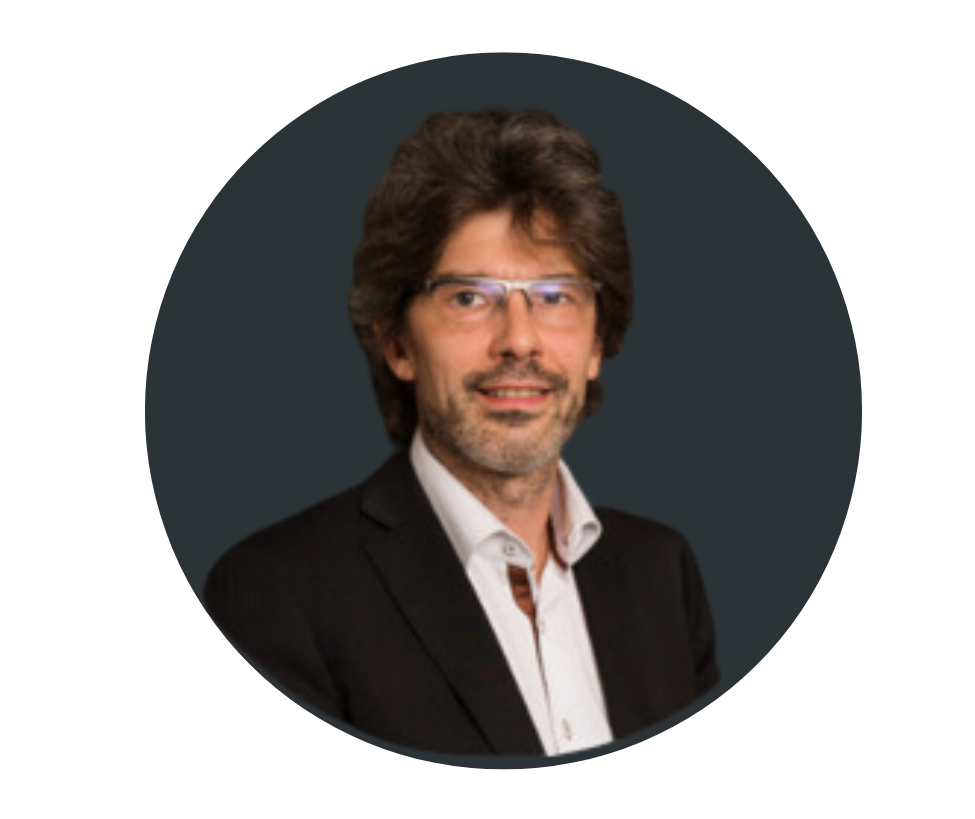
Partner
For almost 25 years, Raphaël has been leading performance assignments in a wide range of industrial sectors (both in France and internationally) to improve processes, conduct purchasing initiatives, implement operational management systems, upgrade managers’ skills and overhaul organizations based on a culture of Operational Excellence. Raphaël is guided by the need to implement change management to ensure a smooth transformation, but also by the challenge of achieving operational results – SQCDME – and thus having a lasting impact on the income statement.
Some of our references
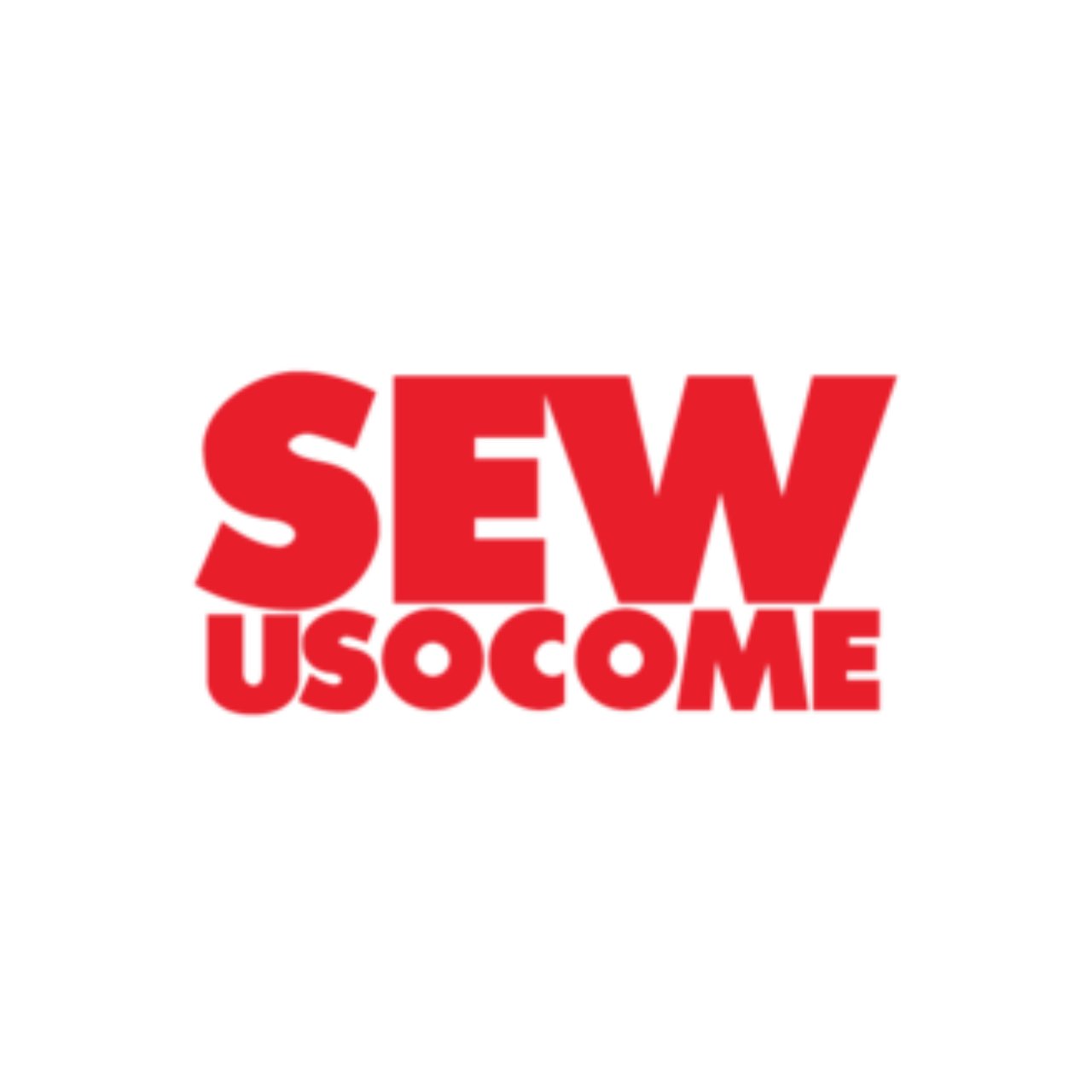
Project management assistance for a new fully automated plant Developing the autonomy of production teams
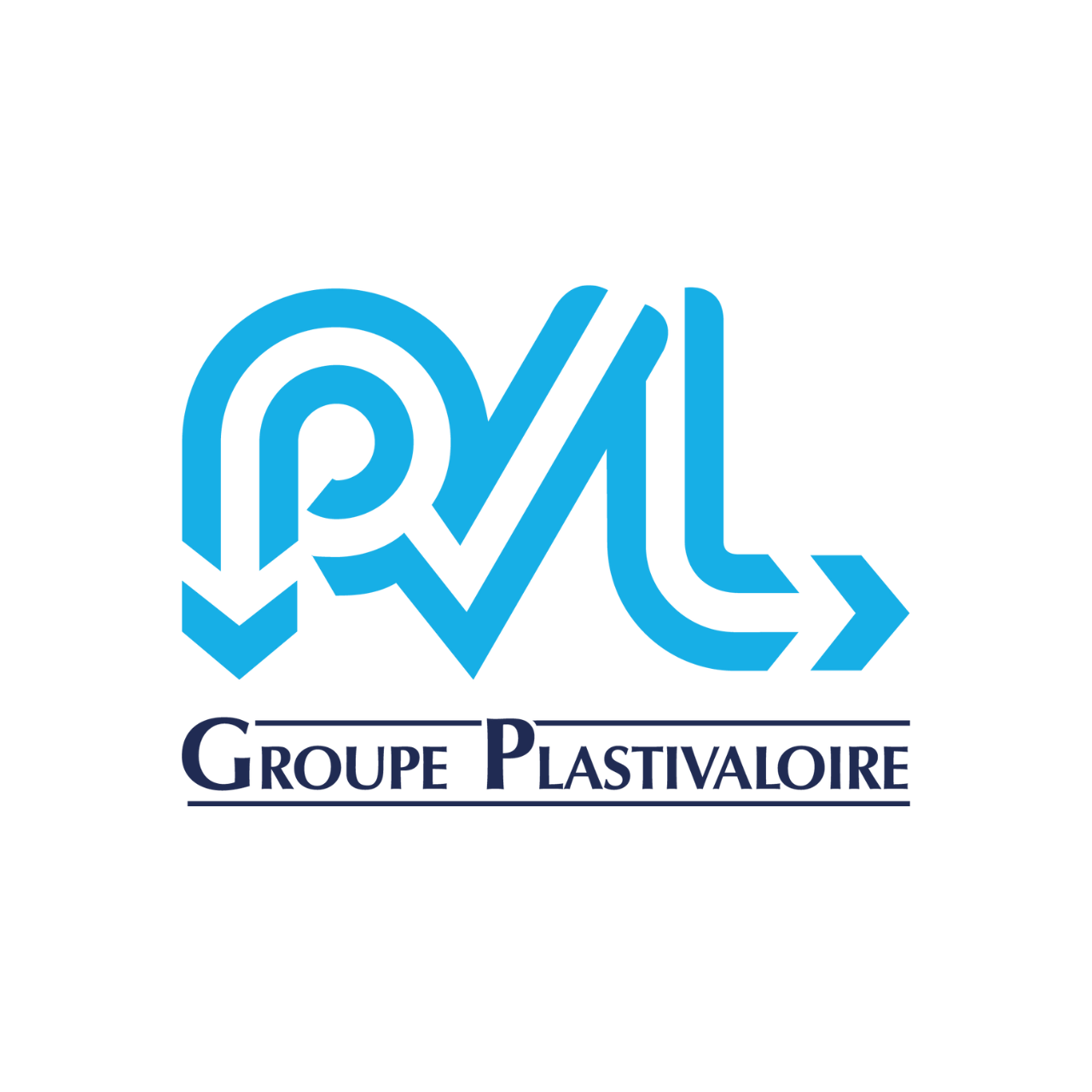
Deployment of new Lean development methods for strategic investments
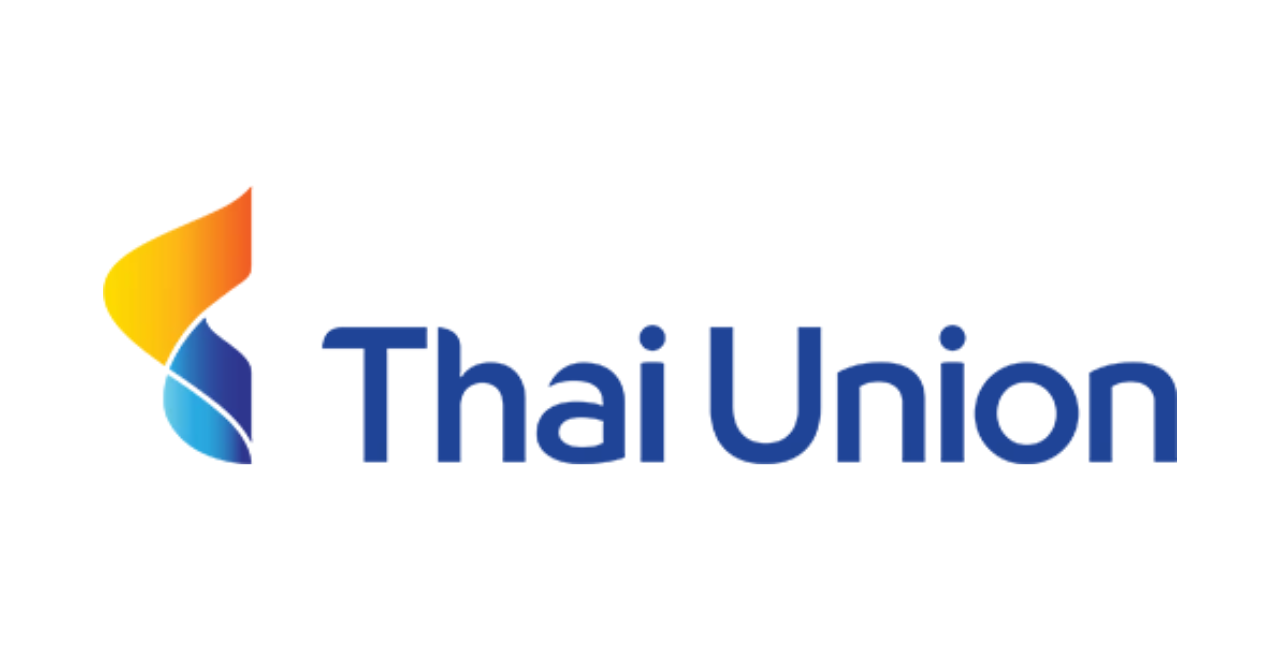
Implementation of product management control and methods for calculating production standards
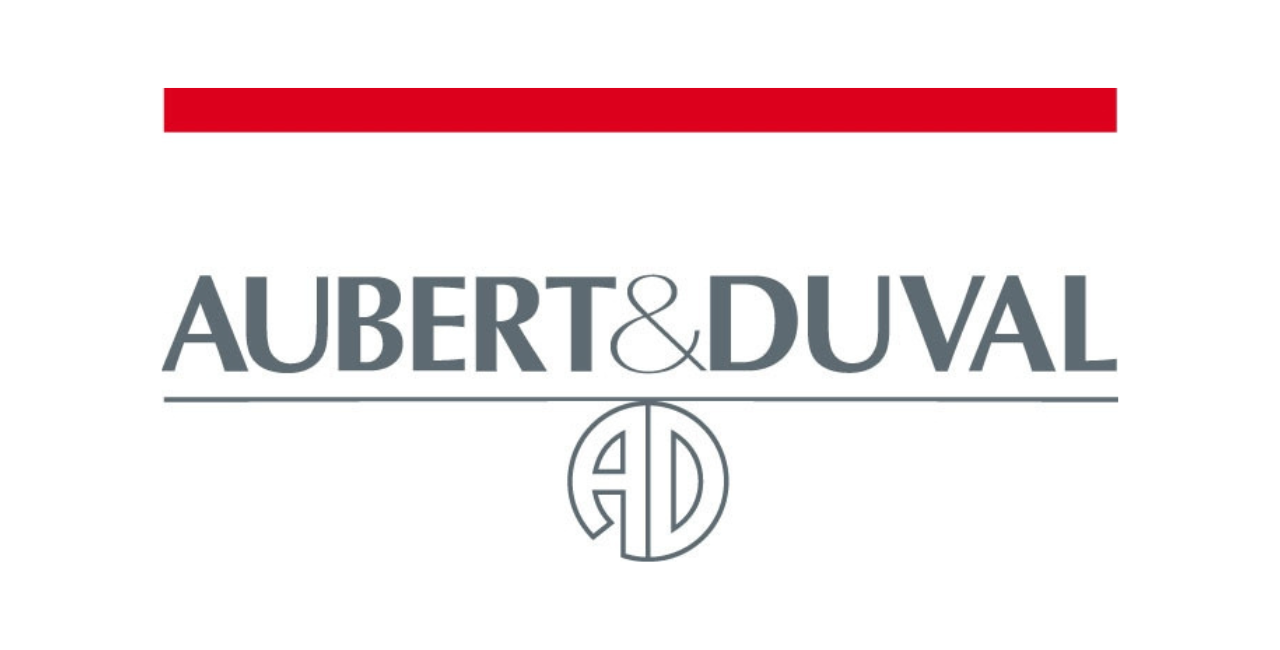
Implementation of multi-site progress plans to reduce lead times and improve quality
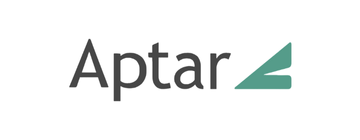
Dematerialization of the quality release file and support for the changeover to the new ERP system
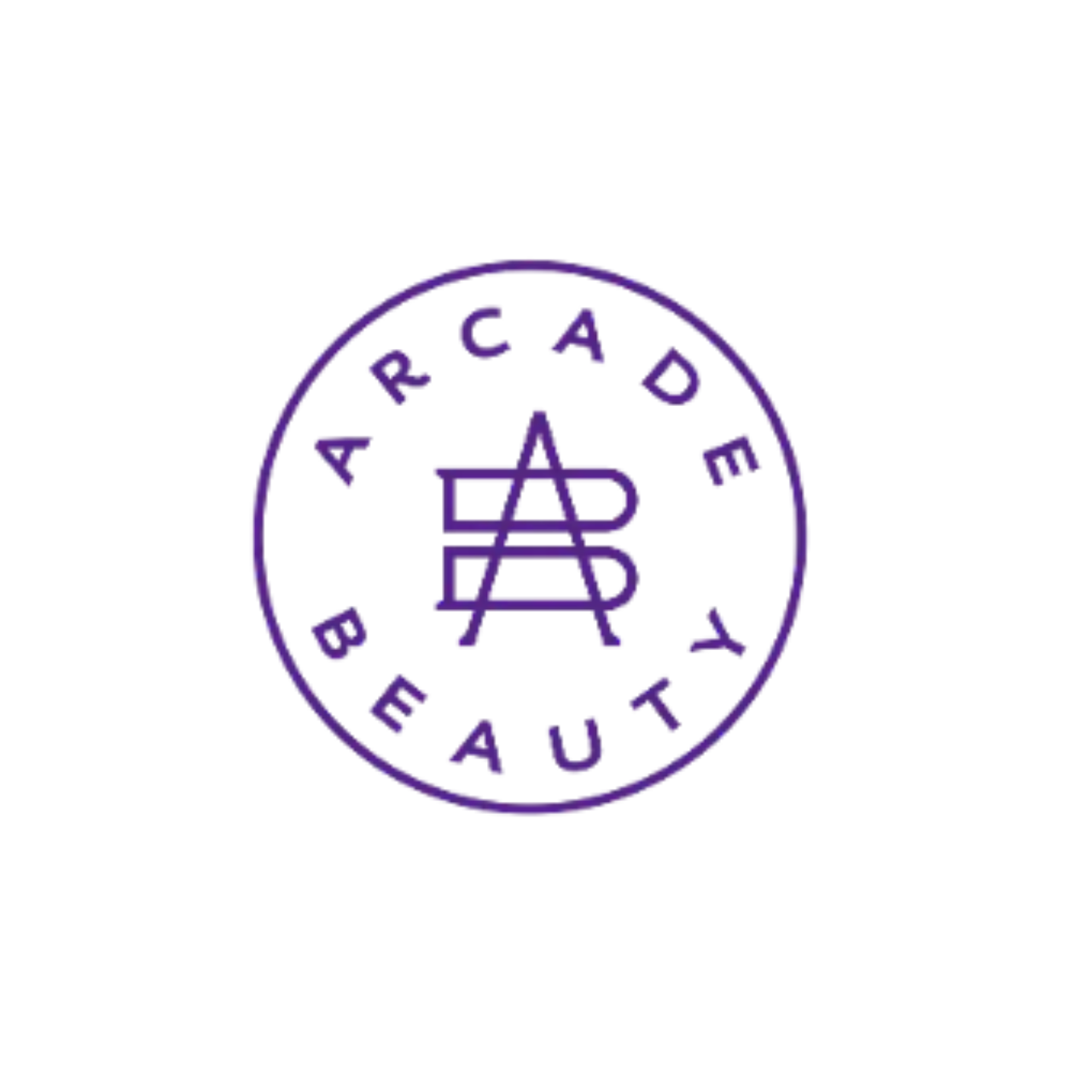
Setting up industrial performance management and developing the skills of first-level managers
They testify
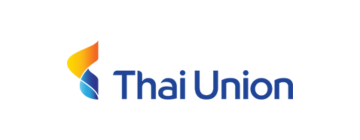
« The joint work between Thai Union sales and industrial management control teams and Citwell has enabled us to structure the management of our costs and the monitoring of our budgets. The tools that have been put in place enable the teams to consolidate data quickly and to devote more time to value-added activities such as identifying levers for improving the cost volume mix. »
Guillaume Kervennal, Thai Union Group Business Unit Director at Meralliance
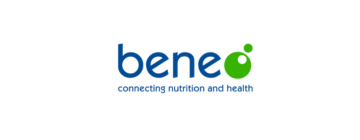
«We chose Citwell to support us in our operational excellence project. The Citwell team is guiding us through an approach that doesn't aim to make us perfect, but to make us better than we were yesterday. And as a perfectionist, this has enabled me to evolve, limit the obstacles and move forward more quickly. »
Cécile Gaillard, Operationnal Excellence Manager at Beneo
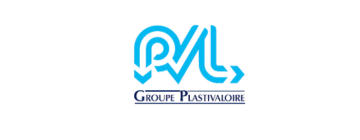
« Citwell's manufacturing team perfectly understood and mastered the mission, which was not limited ‘simply’ to reducing our investment costs on a project. Our ambition was to change our organizational model; Citwell helped us achieving this objective by generating real gains in performance and efficiency. »
Antoine Doutriaux , Plastivoire managing director
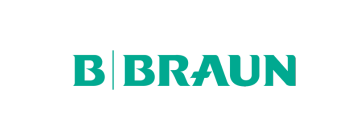
« Citwell really does recommend the technology you want, not just a few technological bricks wrapped up in a big dose of lean. »
Martial Debray , OPEX Manufacrtig OPM & France B.Braun Medical Director