Logistic & Industrial Network Design
Logistics is entering a new era. With the significant evolution of customer demands, the democratization of new technologies, the rapid rise of environmental awareness, and the increasing challenges in resource availability and motivation, the challenges are immense, and modernization initiatives are numerous.
Your stakes
With advancements in technology, increasing customer demands, and financial pressures, companies need to optimize their logistics and distribution networks while also reducing their carbon footprint—a major new challenge. Additionally, mergers, acquisitions, and restructuring efforts often necessitate a comprehensive reevaluation of the global network and product allocations to ensure alignment with new business strategies and operational efficiencies.
Supporting the customer service offer
- Align network architecture with your service offering.
- Differentiate service policy according to products and customers.
- Balancing inventory to meet service quality targets.
- Allocate markets and customer types to different distribution sites.
Optimizing operations
- Resize network and network sites to adapt to changes in business activity.
- Ensure that industrial capacities are strategically located and production costs are optimized.
- Optimize operating costs, including distribution, transportation, and investments in new sites or storage facilities.
- Assess how product ranges align with manufacturing locations and their associated factories.
- Optimizing the network following disposals or mergers.
- Assessing the robustness of the network in the face of risks - "what-if" or "stress test" scenarios.
- Simulate strategic sourcing and distribution decisions.
Improved economic performance
- Increase revenues and operating margin.
- Optimize supply chain operating costs and limit capital expenditure.
- Reduce working capital requirements (WCR) and improve Return on Capital Employed (ROCE).
- Optimizing the use of existing resources.
Our convictions
A comprehensive, shared strategic vision
- Build the Supply Chain offer with players who know their markets and customers.
- Consider the strategic plan, with developments by market, by site, by product family.
- Compare alternative scenarios with the current organization projected in a given future context.
A cross-functional approach within the organization
- Thinking beyond the Supply Chain: a company-wide approach.
- Identify constraints and possibilities with the company’s decision-makers.
- Involve key players throughout the project, from scenario identification to evaluation.
Modeling adapted to input precision
- Prefer a modeling approach in line with the reliability of assumptions formulated.
- Adapt the depth of the study to the accuracy and robustness of the activity data.
- Use the best modeling tools on the market, depending on the context.
A pragmatic, costed roadmap
- Decline the target into a succession of steps adapted to the company’s context.
- Cost each stage of the roadmap to build and manage the business plan.
- Propose a complete transformation plan: technical, process and social impacts.
Our solutions
and approach
Looking to enhance your logistics performance to better serve your customers, control costs, and protect the environment? Our expertise covers every link in the logistics chain.
Vision: Seminars, Workshops and Interviews
- Lead seminars to build and validate the strategic vision with members of the management committee.
- Organize workshops and interviews to work on the Supply Chain offer or strategic plan.
Our tools: DCA brainstorming, interview support on various topics, benchmarks
Immersion: Qualitative and Quantitative
- Gather information and understand the existing supply chain network.
Our tools: Questionnaires, Data collection specifications, Flow diagrams and process flow charts, Interview support on various topics, Site visits
Data analysis: "make the figures visual"
- Check the consistency of data supplied using dedicated mass data analysis tools, and aggregate data at the required level.
- Make key elements visible by providing key figures on site activity, flows, transport and inventories.
Our tools: Access and Excel-based data analysis tools, modeling and mapping software, etc.
Market modeling tools
- Broaden the field of possibilities to find an optimum, test complex scenarios, multiply alternative scenarios, calculate isochrones to ensure compliance with the service offer, maximize the use of a particular site, use conditional minimums…
Our tools: “Network Optimization” module, documentation and expert support, Benchmarks
Impact on the organization
- Study the impact on different areas and functions of the company: technical, economic, social, systems, customers and suppliers, etc.
Our tools: RACI, process flowcharts, job descriptions, RFI and RFQ, business cases, ROI calculations, studies of contracts and conditions
Change management
- Guarantee change management in the organization right from the design phase of the future Supply Chain diagram.
Our tools: IMCM reference framework, tectonics of change, communication plan
Your gains
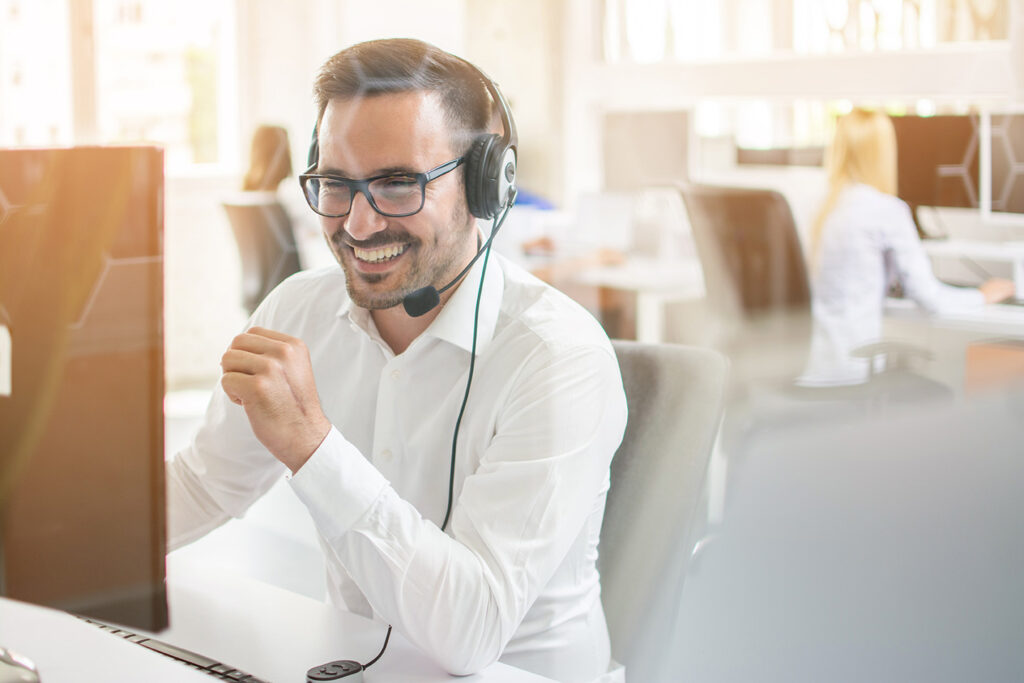
Customer satisfaction
- Improving the definition of and compliance with the service offering
- Increase customer service levels
- Improved stock availability and utilization
- Reduce Time To Market
- Simplify sourcing and transport policies, and thus reduce the complexity of flow diagrams for teams.
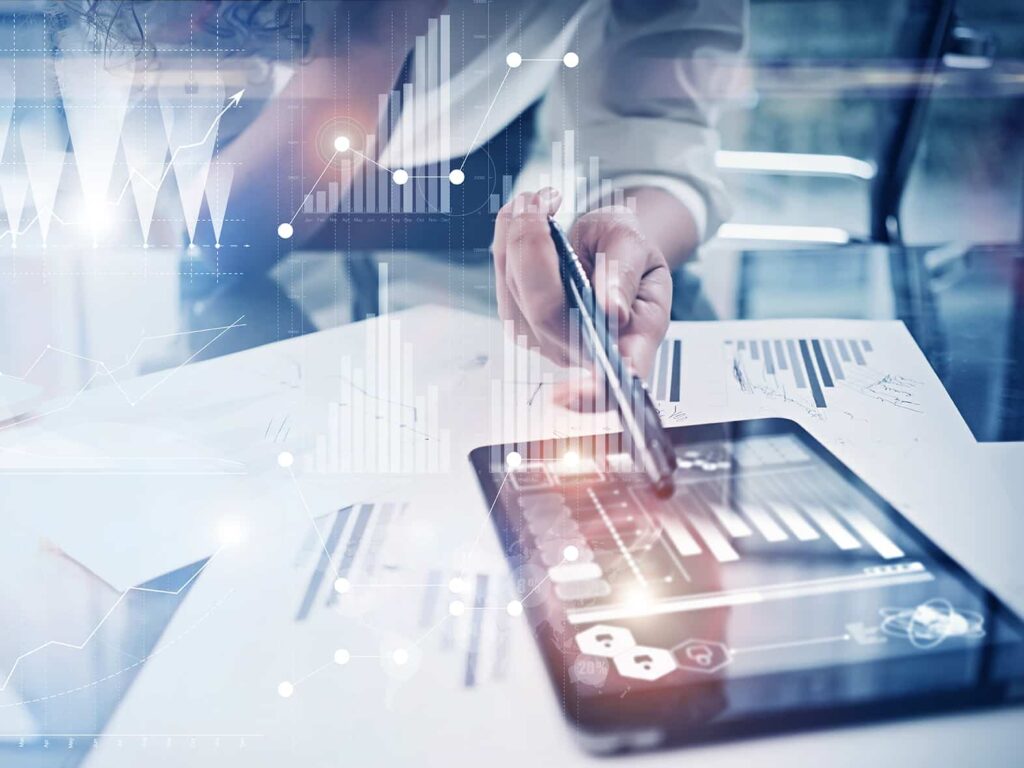
Revenue and margin
- Increase in revenue at isoperimetry
- Growth through new markets and distribution channels
- Margin improvement (gains on purchases or distribution linked to the switch via hub from dispatch …).
- Invoice services (express, premium) at fair value to help boost margins.
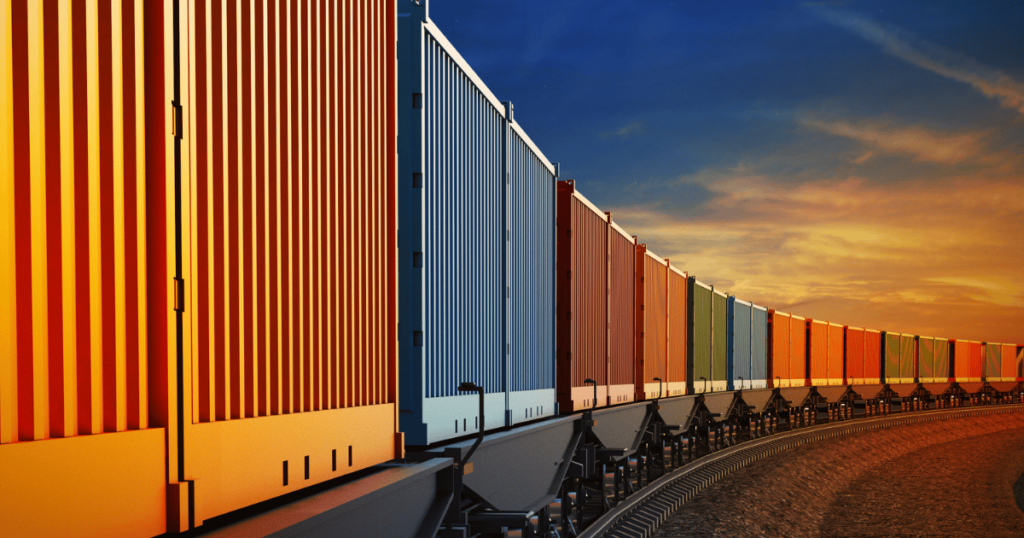
Supply Chain cost
- Optimizing transport costs
- Lower logistics costs
- Risk management, continuity planning
- Reduced air travel, lower transport costs and smaller footprint environment
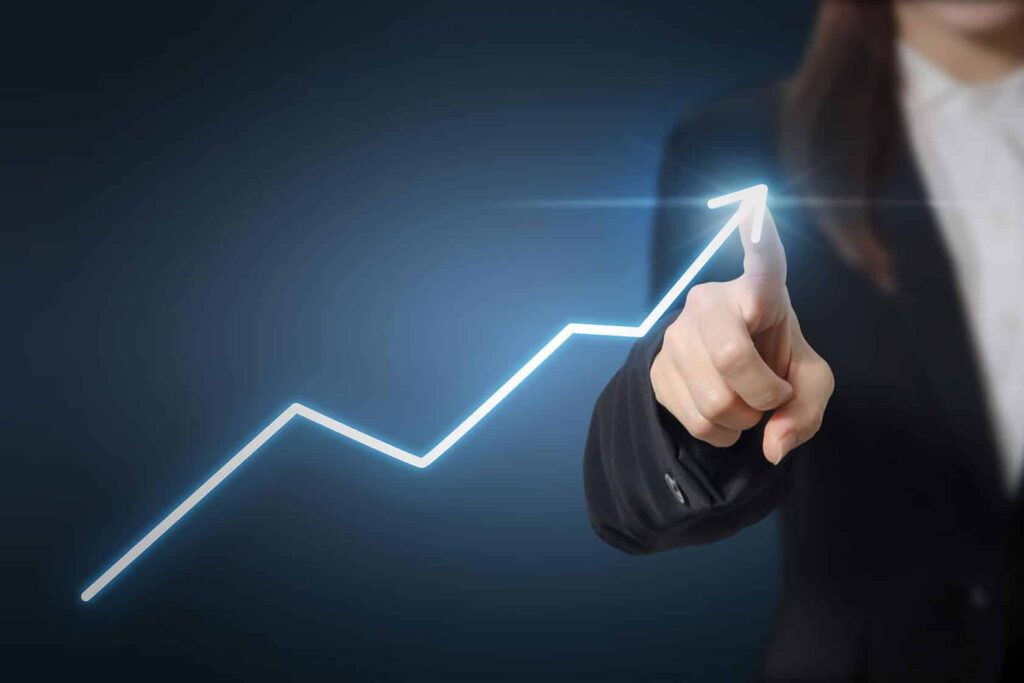
WCR optimization
- Inventory write-downs: financing and obsolescence depreciation
- Rationalization of existing assets
- New investments with controlled ROI
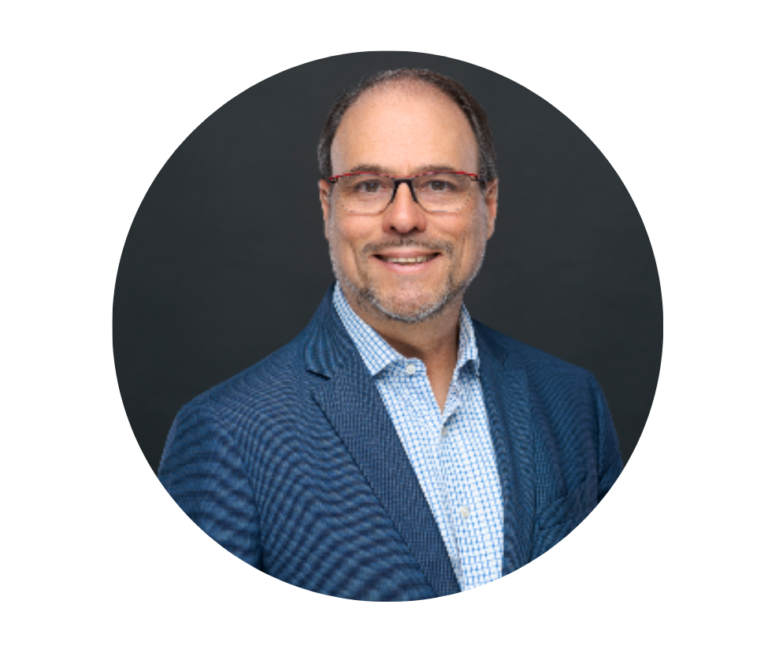
A project? Contact us
Group Managing Director and USA CEO
Laurent Penard, a founding partner of Citwell and a graduate of École Centrale, has been in the consulting industry for over 30 years. He started as a consultant with major international firms and founded Citwell in 2004. Alongside his role as the firm’s CFO, Laurent leads diagnostic assessments and supply chain transformation projects for both SMEs and large corporations in the industrial, retail, and service sectors.
In 2024, he decided to focus on expanding Citwell internationally and took on the role of President of Citwell US at the Boston office. He then passed the chairmanship of the group to Guillaume Allemand.
Among our references
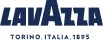
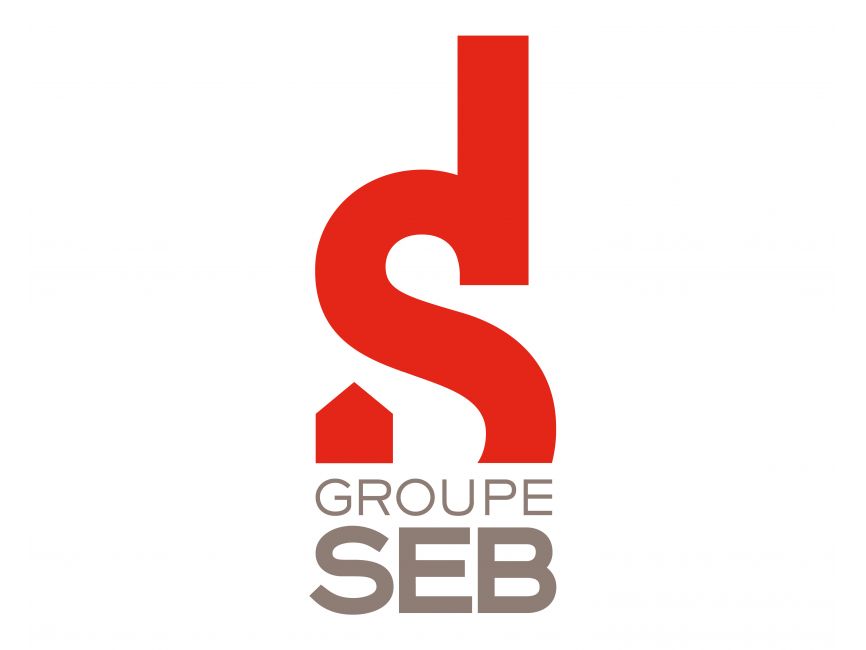
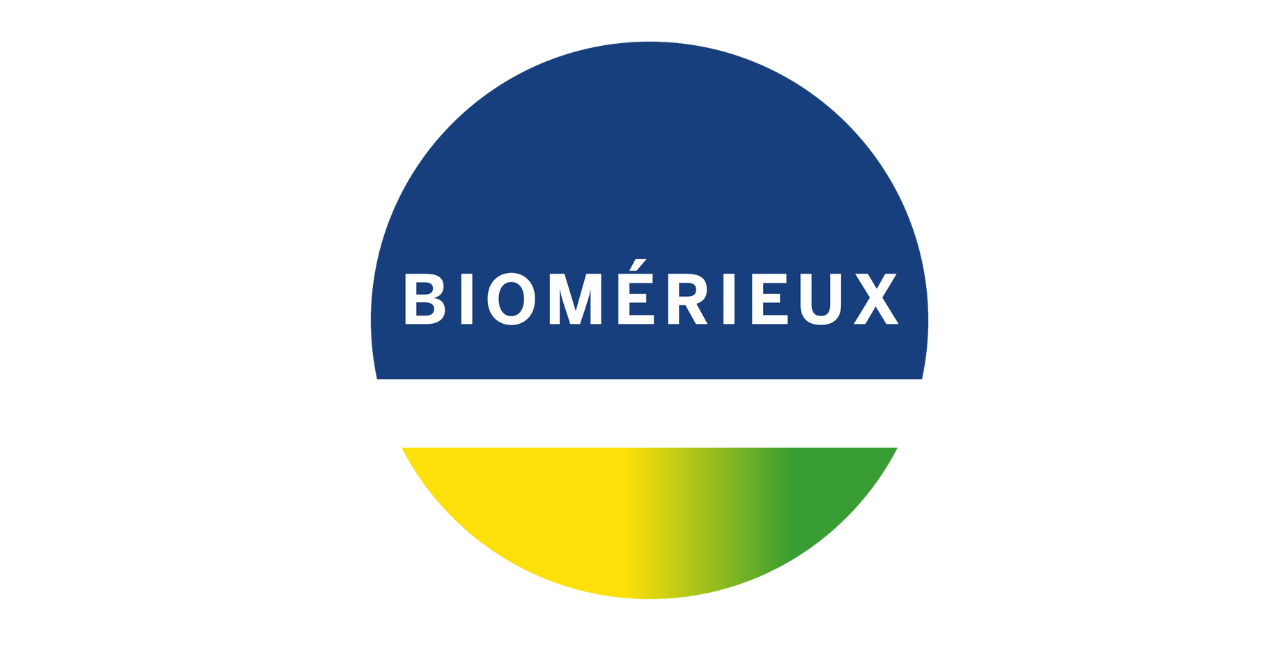
Business Case
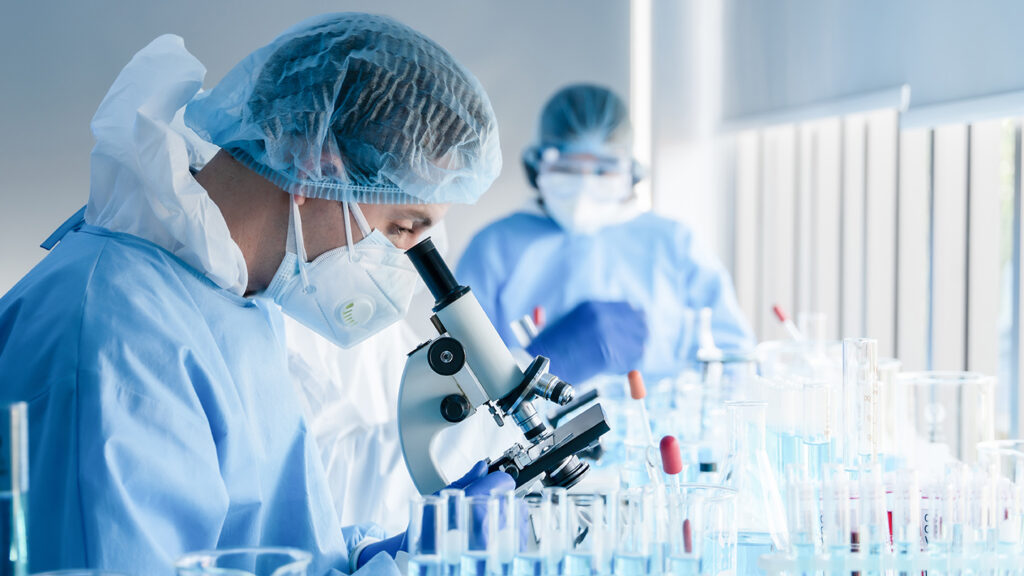
Support for an crisis unit logistics and health resources in a public administration
About:
An important French public administration prepares and implements government policy in the fields of solidarity, social cohesion, public health and the organization of the healthcare system. It is responsible for the organization of prevention and care. It draws up and implements, in liaison with the other relevant ministries, the rules relating to health protection policy against the various risks likely to affect the population. It sets up the necessary management structures in the event of a health crisis
Challenges:
As part of the COVID-19 health crisis, this public administration set up a health crisis center, including an interministerial logistics crisis unit, to manage the supply and distribution of protective equipment for healthcare professionals, as well as certain drugs under pressure, adressing critical industrial operations.
The state faced several major challenges:
- The limited availability of equipment at the start of the crisis made it necessary to set up a penurious management system and target professionals in urgent need of equipment.
- A monthly Demand Driven S&OP (DDS&OP) routine.
- Lack of a centralized information system to calibrate distribution.
- Operational logistical resources ill-suited to the scale of the crisis.
The main objective was to serve healthcare professionals dealing with COVID-19 patients as quickly and effectively as possible.
Citwell’s Involvement:
- Set up an initial, extremely rapid equipment distribution system to healthcare professionals as a matter of urgency.
- Identify available distribution networks that can be activated in times of containment.
- Participate in determining a distribution doctrine by means of a scenario for this public administration’s office.
- Control the supply of domestically-produced equipment imported by air.
- Integrate equipment sourcing information.
- Help structure the organization of the crisis unit.
- Set up management processes and reporting systems.
- Draw up stock projections enabling this public administration’s office to establish its purchasing and management policy.
- Coordinate another public administration, responsible for distributing materials to healthcare professionals.
- Create a system for managing resuscitation drugs in high-demand situations to ensure their availability throughout the crisis.
Results:
- Activation of two distribution channels, Territorial Hospital Group and Officines, for weekly high-volume distribution based on theoretical consumption per healthcare professional.
- Weekly doctrine proposals and operational implementation monitoring.
- Assisting the Crisis Unit management in certain decision-making processes and communicating with ministerial cabinets.
- Regulating tension on drugs at risk of shortage.