Depuis quelques années, une vague puissante de changement submerge le monde des usines : l’industrie s’hybride avec le numérique et donne naissance à un nouveau paradigme dans lequel service et produits se combinent pour répondre à l’évolution du monde industriel. Comme dans toute transition entre deux mondes, le changement ne se fait pas du jour au lendemain, les deux mondes cohabitent. Les nouvelles technologies s’intègrent de manière plus ou moins rapide selon le secteur d’activité et niveau de maturité de chaque industriel.
Les nouveaux défis pour le monde industrielLe premier défi étant celui de l’hyper connexion : connexion des machines, des hommes, des produits. L’information n’est plus limitée à quelques-uns et les équipes sont en demande de sens et d’autonomie. La valeur clé est la réactivité dans la prise de décision même au sein des ateliers de fabrication. Le second défi est l’exploitation des données industrielles, des quantités considérables de données sont disponibles, les puissances de calcul sont, chaque année, multipliée et les technologies industrielles suivent cette tendance. Il faut donc faire preuve d’agilité pour tirer en permanence le meilleur profit de l’évolution de la robotique industrielle et des outils numériques.
Le troisième défi est celui de l’hyper concentration, le domaine du numérique est maîtrisé par les plus gros acteurs, mais de nombreux nouveaux acteurs apparaissent. La valeur clé est donc la connaissance et la maîtrise de son éco-système. Les directions industrielles et SI doivent savoir bien s’entourer pour faire le choix d’un partenaire dans l’avenir et pour définir le meilleur moyen d’intégration de la solution. Enfin l’évolution de la perception de la valeur fait aussi son entrée dans le monde industriel, le produit était la valeur principale il y a encore quelques années. Les données de ventes et de comportement client sont déjà exploitées pour créer des services innovants. Mais nous allons petit à petit vers une exploitation des données industrielles qui permet d’améliorer les processus et la prise de décision notamment via l’intelligence artificielle.
Le modèle Tesla : modèle organisationnel pour le monde industriel ?Le Teslisme aussi appelé modèle tesla bouleverse les codes des organisations industrielles en proposant un modèle basé sur 7 principes qui semblent répondre aux défis stratégiques et technologiques. Un de ces 7 principes est l’hyper-manufacturing qui permet d’augmenter le système industriel pour le rendre agile, customisable et générateur de valeur collaborative.
La rapidité et l’agilité du processus de fabrication sont les clés de cette organisation qu’on peut aussi identifier comme une montée de version du lean manufacturing. L’objectif majeur se résume par le fait de combattre tous les freins liés à la création de valeur collaborative. On retrouve dans l’hyper manufacturing des activités liées à la diminution de l’empreinte carbone du produit de bout en bout. L’optimisation des processus de production (pour ne pas gâcher la matière première), éviter les rebuts et piloter la consommation énergétique.
Les nouvelles technologies permettent de répondre à ces deux piliers du Lean (juste à temps et bon du premier coup). Nous pouvons citer notamment les progrès de la robotisation tels que les AGV, l’impression 3D, les systèmes de détection des défauts dans le flux de production, les objets connectés (IOT) qui permettent une identification unitaire des produits. Des solutions pour le pilotage de la production tel que les MES qui permettent de transmettre les informations et de les exploiter de manière collaborative.
Le MES (Manufacturing Exécution System) : un moyen d’assurer la continuité digitale dans l’usine ?La donnée est l’or noir de la 4ème révolution industrielle. Ne pas récolter, stocker ou analyser la donnée dont on dispose que ce soient des données client ou de la donnée industrielle freine largement la valeur que l’on peut créer pour la société. Cela peut avoir des conséquences sur l’efficience du processus, mais aussi sur la qualité du flux. Il est nécessaire d’exploiter les données pour identifier les problèmes et les causes tout en ayant une logique d’apprentissage permanente. Le travail en silo freine également la vitesse à laquelle l’information circule et génère des décisions contreproductives.
Avec le digital chaque service à besoin de s’inviter sur un périmètre qui était en dehors de sa frontière pour contribuer à la valeur globale. Par exemple, la fonction qualité à besoin de connaître les paramètres machine et les causes des pannes pour pouvoir trouver les causes de non-qualité et faire des corrélations entre tous ces paramètres. Il n’est d’ailleurs plus rare de voir que l’exploitation des données industrielles est réalisée via l’IA, les algorithmes de Machine Learning peuvent alors identifier ces liens de façon plus ou moins supervisée, pour pouvoir prédire meilleurs paramètres process.
Les solutions MES permettent de suivre la production, de surveiller et synchroniser l’exécution de processus physiques en temps réel de la matière première jusqu’au produit fini. Ils coordonnent l’exécution et permettent l’exploitation des données collectées tout au long du processus que ce soit sur les temps d’arrêt, les causes de rebuts, la traçabilité des lots et les historiques de paramètres machines.
Les points clés d’un projet MESLa solution MES vient faire la passerelle entre les données terrain avec les outils de pilotage souvent présent dans les industries l’ERP, le WMS et la GMAO. L’objectif est de fondre ces silos pour avoir au sein d’une même application les données, les alertes en temps réel et surtout partager et exploiter l’information dans une démarche d’excellence opérationnelle.
Une des premières étapes dans un projet MES est l’analyse des processus, la formalisation des relations entre la production et les autres fonctions de l’entreprise sont essentielles pour identifier le degré de maturité de l’entreprise. Cette étape d’étude préliminaire permet d’éviter de faire le choix d’une solution qui ne sera pas adaptée aux métiers et processus de celle-ci.
La clé vient du fait de piloter le projet MES comme un projet lié à une démarche d’amélioration continue, il faut avant tout penser au processus d’exploitation des données et d’amélioration continue associés qui permettra de réellement gagner des points de performance. Trop souvent les projets MES sont vu comme un projet outil alors qu’ils doivent servir de support à l’excellence opérationnelle.
Puis arrive le choix de la solution n’est pas l’étape la plus facile, le choix dépend de votre objectif. Qu’essayez-vous d’accomplir ? Qu’est-ce qui constitue un bon outil de pilotage de l’exécution ? Comment devriez-vous utiliser la technologie pour améliorer vos processus décisionnels ? C’est notamment dans ce cadre que nous accompagnons nos clients pour les guider vers des solutions qui répondent à leurs besoins fonctionnels. Ce n’est pas le choix d’un logiciel, mais plutôt le choix d’un partenaire qui saura répondre aux exigences du processus et que ce soit en termes d’ergonomie sur les postes ou pour faciliter l’exploitation des données collectées. Le travail en collaboration avec les technologues pour mettre à l’essai, apprendre et évoluer via la mise en place de POC (Proof of concept) est aussi un levier pour assurer la sélection.
Xavier Gabard, Manager, Groupe Citwell
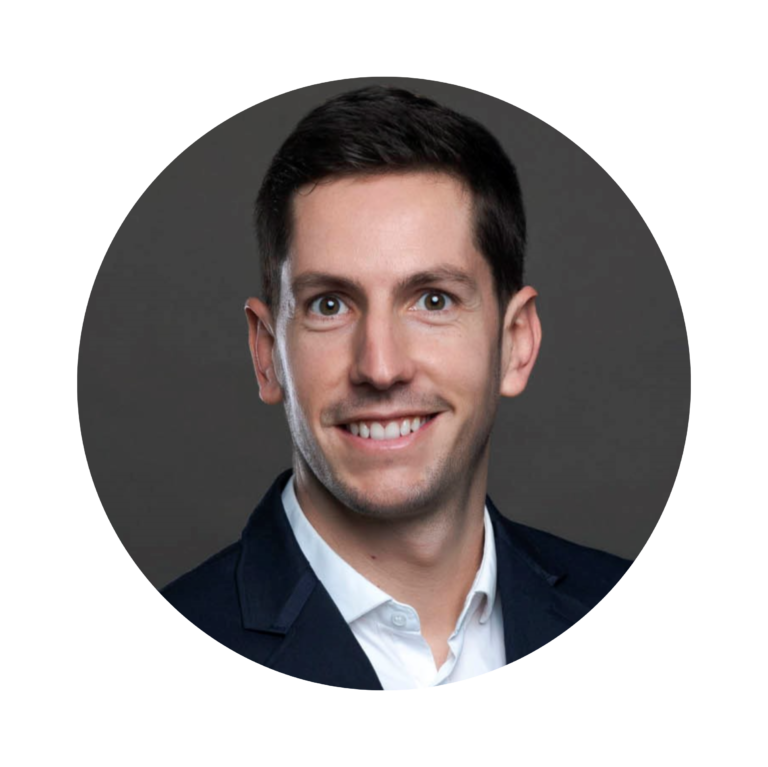
Un projet ? Contactez-nous
Manager
Diplômé des Arts et Métiers, Xavier a 12 ans d’expérience professionnelle chez des industriels en tant que chef de projet Supply Chain et amélioration continue. Il a accompagné différentes améliorations d’excellence opérationnelle : en production, logistique et supply chain en France et à l’étranger notamment en lien avec l’univers de la GSB.
Ses accompagnements concernent à la fois l’identification des pistes de progrès, la définition des plans de performance et le pilotage des projets de mise en place.